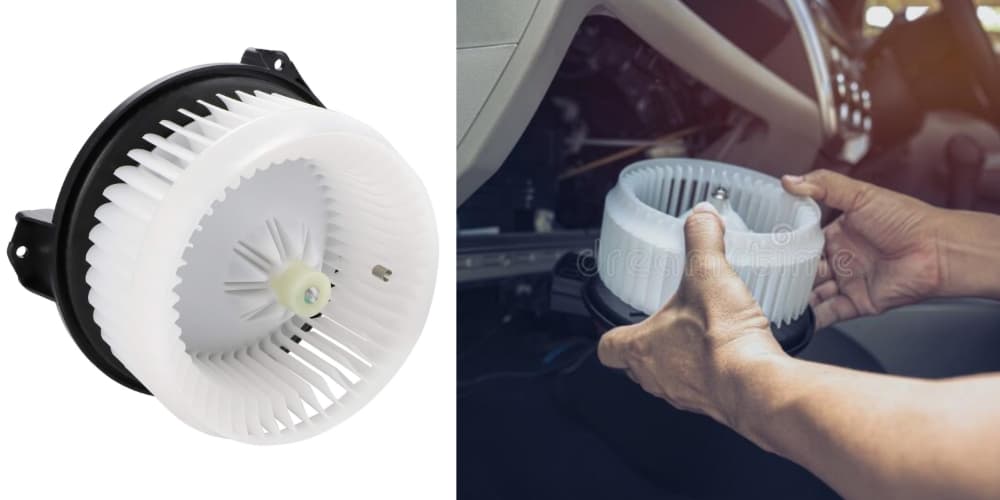
Just like that one lazy colleague of yours, you might find that your car’s blower motor doesn’t work all the time, especially when you really need it to.
This can make it challenging to change the temperature and air quality inside your vehicle. While this doesn’t really affect the safety of your car, it can be a source of discomfort.
Car blower motors can work intermittently for various reasons, including broken or damaged wiring, worn brushes in the motor, debris obstructing the motor, and many other mechanical and electrical failures.
Troubleshooting a car motor blower can take some time — it’s a process of elimination. If you have some electrical or mechanical experience, you might have an idea where to start, but I would encourage you to read on for some tips on solving problems with this system.
1. Broken or Damaged Wiring
An intermittent failure can be much more difficult to troubleshoot than an outright failure. Usually, when something breaks, you just replace the component.
Still, the blower motor is part of a more complex system that contains various circuits, selector switches, and of course, the motor and fan itself.
An intermittent blower motor can do all kinds of strange things. It might work fine for a while, only to stop working or perform erratically, speeding up and slowing down.
For instance, the speed selector switch or other related control may be defective or worn, resulting in the blower working inconsistently.
A poor connection will result in your blower working seemingly randomly. If you have to smack your dashboard in a specific place to get it going, you might be dealing with broken or damaged wiring, especially if it stops randomly.
Electrical issues are among the most common and troublesome faults one can have. They can take a long time to trace to the source since wires often run through small channels and crevices.
In this case, most of your wiring will be obscured by your dashboard. It will either be accessible by removing panels, the instrument cluster, or through the footwell, depending on your vehicle.
Wiring can degrade over time when exposed to heat, moisture, and friction. When contact points become corroded, it increases the resistance in the circuit.
Heat is a byproduct of resistance and can, under some conditions, melt or damage insulation. Damaged insulation causes short circuits and can cause intermittent blower motor operation.
How To Fix
Inspecting the wiring between your blower motor and control panel is an excellent place to start. Still, it often involves extensive stripping to access the harness.
There can also be other components in the system that fail and make poor contact, such as resistors and capacitors. Where these are found, they should be carefully inspected to make sure they are firmly connected. Any signs of burning or corrosion should be noted.
Burnt or corroded components should be replaced, and this requires a degree of skill since they often need to be desoldered and replaced.
If you don’t know what you are doing, you can damage circuits by overheating them. It’s best to contact a qualified auto electrician if you are uncomfortable doing solder work.
2. Worn Brushes in the Motor
Most electrically driven motors contain brushes that drive them, taking advantage of the force of magnetism and the effects of polarity to create the rotation that blows air into the cabin of your vehicle.
These brushes are essential to the operation of electrical motors. However, they become worn over time, necessitating their replacement.
Worn brushes in your blower motor can cause intermittent function. They may operate under some conditions, like when you first activate the blower. They degrade as the blower warms up and expand away from the magnets.
How To Fix
If you suspect failing brushes are causing your blower motor to function abnormally, you’ll have to strip it out of the vehicle and service it. You will need to replace worn brushes.
Blower motors will vary by vehicle model and manufacturer, so you will have to determine what replacement parts are available by finding a manufacturer part number.
You may also be able to find information on online forums for your particular vehicle or purchase a service manual if you want to do it yourself.
3. Debris in the System
Manufacturers do their best to design cooling systems so that dirt and debris do not get into them. Still, invariably things can get through and sometimes block the fan.
This is usually accompanied by a cacophonous din emanating from where you want air to be coming from.
Debris can penetrate your cooling system and build up in or around the fan. If dirt and debris accumulate within your cooling system, it can obstruct the fan and prevent it from turning.
It may occasionally become dislodged, allowing the motor to turn and creating an intermittent fault.
If a fan stops working and then suddenly starts up again, you may have a broken fan whose pieces can get lodged and dislodged, causing an apparent intermittent operation.
How To Fix
The motor should be inspected and cleaned — dirt accumulation can cause premature failure.
The ducting and components will also have to be cleaned out for regular operation to resume. In addition, you must inspect the motor bearings and filters.
Take a Look at Your Motor Bearings
If dirt has accumulated in your ventilation system, this can be bad news for the service life of your motor.
Bearings will be discussed in greater detail later in the article since they can also fail and cause the intermittent function of the blower motor.
To prevent premature failure, once you have cleaned your dirty ventilation system, it is prudent to inspect the motor to ensure that the fan turns freely without any binding.
To check, rotate the fan gently by hand. You might notice a little resistance, but will likely be no grinding or binding.
Never spin the fan — you only need to rotate it slowly through its range of motion.
Check Your Filters
This goes hand in hand with dirt in your system — some vehicles are fitted with filters for their air ventilation. If these get clogged up, you may experience signs of premature motor failure.
Refer to your vehicle’s owner’s manual. If it contains a filter in the air system, there should be either instructions to replace it or a service interval indicating how often it should be changed.
If you live in a dusty area or travel dirt roads frequently, as a rule, you should be changing your filters more often.
This includes engine air filters and oil filters. Note that the service intervals supplied by manufacturers tend to assume that vehicles will predominantly be used in an urban setting where roads are paved.
If you do not have access to your owner’s manual, online forums are a tremendous resource. Chances are someone else out there has had a similar problem to what you are experiencing.
You can also learn from the discourse between knowledge seekers and those more familiar with the specifics of a vehicle’s cooling system.
4. Bearing Failure
Bearings are a mechanical component that facilitates movement, in this case, the rotational force of the fan. Typically, motors consist of a shaft onto which the fan is attached and will employ bearings to allow for free and smooth rotation.
If your fan motor’s bearings become corroded due to moisture and dirt, they can fail and seize. The fan may spin intermittently, but its operation will be rough.
Bearing failure is usually evidenced by a grinding noise when the blower motor is active. When it gets hot, it may bind and seize, ceasing to blow air.
The bearings will need to be replaced — this will sometimes necessitate replacing the entire motor where parts are unavailable or in sealed units.
How To Fix
Again, due to the general nature of this guide, it is difficult to talk about specifics since there is such a wide variation in the types of motors that are used.
Manufacturer service manuals are your most valuable resource, but they may not offer specific instructions on replacing blower fan bearings.
Before you set your heart on replacing the blower motor bearings, weigh up your options on replacing the motor itself. Seized bearings can strain the motor and cause other damage that will lead to premature failure.
If you do replace the blower motor bearings, be sure to test the motor to ensure that it is within specified parameters and is not drawing too much current.
If you do not have the equipment to test a blower motor, you can take it to a local auto electrician to test it for you.
Depending on how long your motor has had bearing issues, there may be other damage that has accumulated, so replacing the bearings only solves the original issue. Reinstalling a defective motor is not advised.
Conclusion
Electrical issues have been the source of many headaches since the advent of motorized transport. Modern vehicles are high-tech and more complex, so there is more to worry about.
Still, thankfully the blower motor is typically a straightforward system. With this guide, you should at least have an idea of where to start.